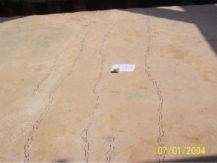
Marked cracks on the tunnel slab
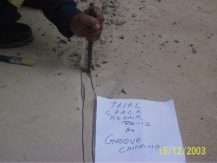
Chipping the grooved cracks
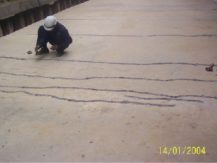
Providing bunds ranging from 0.4 mts. to 0.8 mts. c/c distance

Pouring monomer grout alternatively in the groove
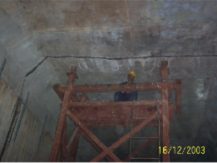
Crack sealed from bottom, leaving one weep hole in the corner
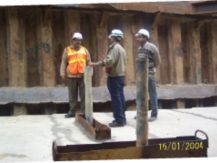
Crack being Hydrotested after repairs
Make OR Break Factor
The thickness of the concrete slab varied from 0.7 mts. to 2 mts. and extreme diligence had to be exercised to ensure material penetration throughout the cracked concrete.
THE CHALLENGE :
- The underground tunnel was facing water leakage issues due to shrinkage and thermal cracks in the deck slab.
THE ODDS :
- Extreme climatic conditions to work in
- Imperative condition was to test cracks for water tightness pressure of up to 6 kg/cm²
OUR RESPONSE :
- The improvised site-specific system was designed for to repair cracks
- All material and systems were developed so as to enable us to grout against the pull of gravity
- All material used was modified to work across diverse summer and winter conditions